MANUFACTURE PROCESS
Manual Handcrafted Insoles, currently known as Goodyear Welted
The traditional manufacturing method “Manual Artisan insole” stands out for its enormous comfort, with advantages in terms of breathability, flexibility, insulation against cold and heat, and great durability.
It also has the advantage of being easy to repair, which we guarantee.
Its articles are developed by hand through manual and high-quality production processes, carefully and demandingly choosing the materials it uses, always opting for natural products and bearing in mind environmental awareness combined with comfort of use.
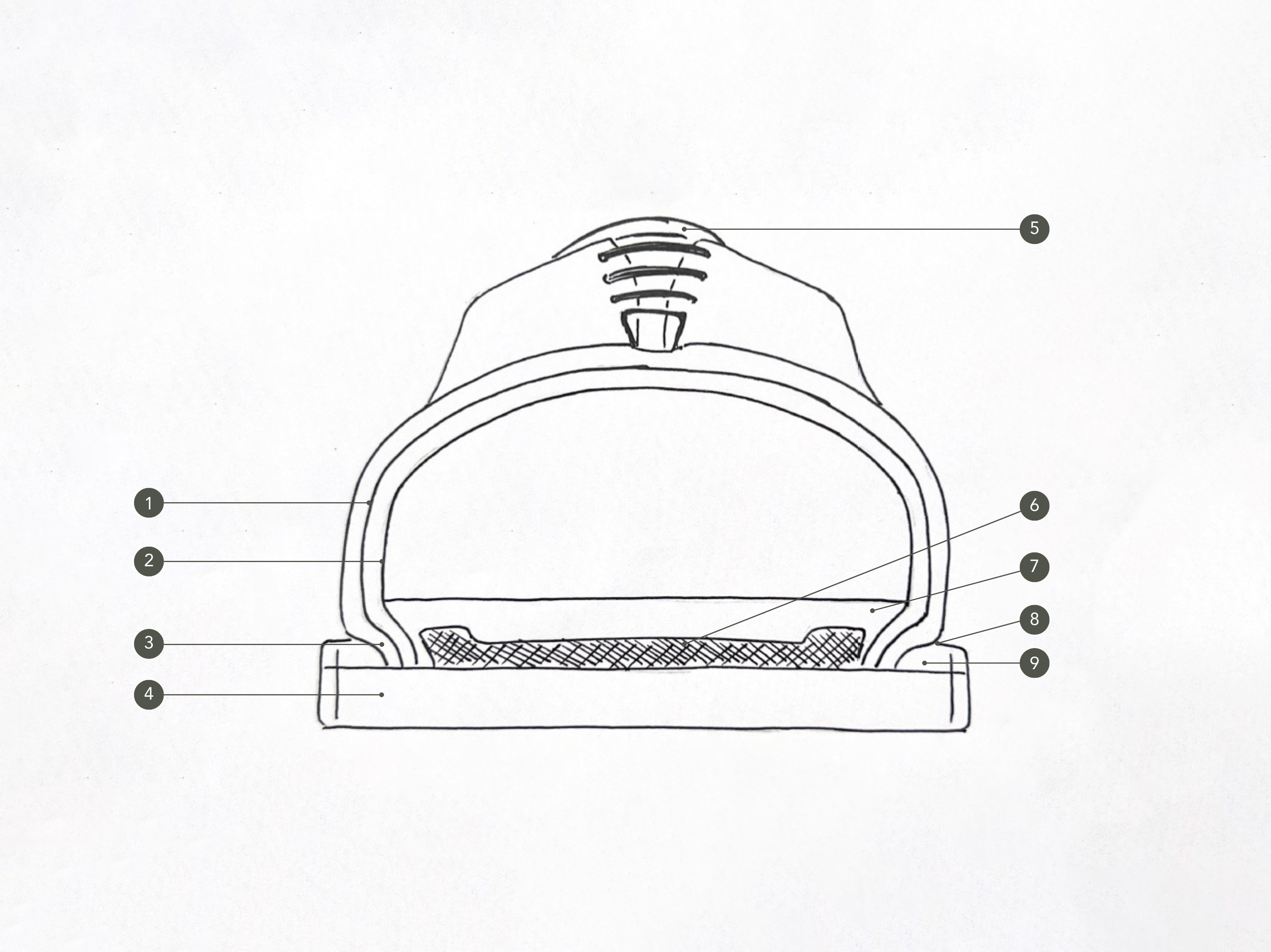
1. Upper
2. Lining
3. Sewn Insole
4. Sole
5. Language
6. Cork Insulation
7. Insole
8. Sewn from the Sole
9. Flip
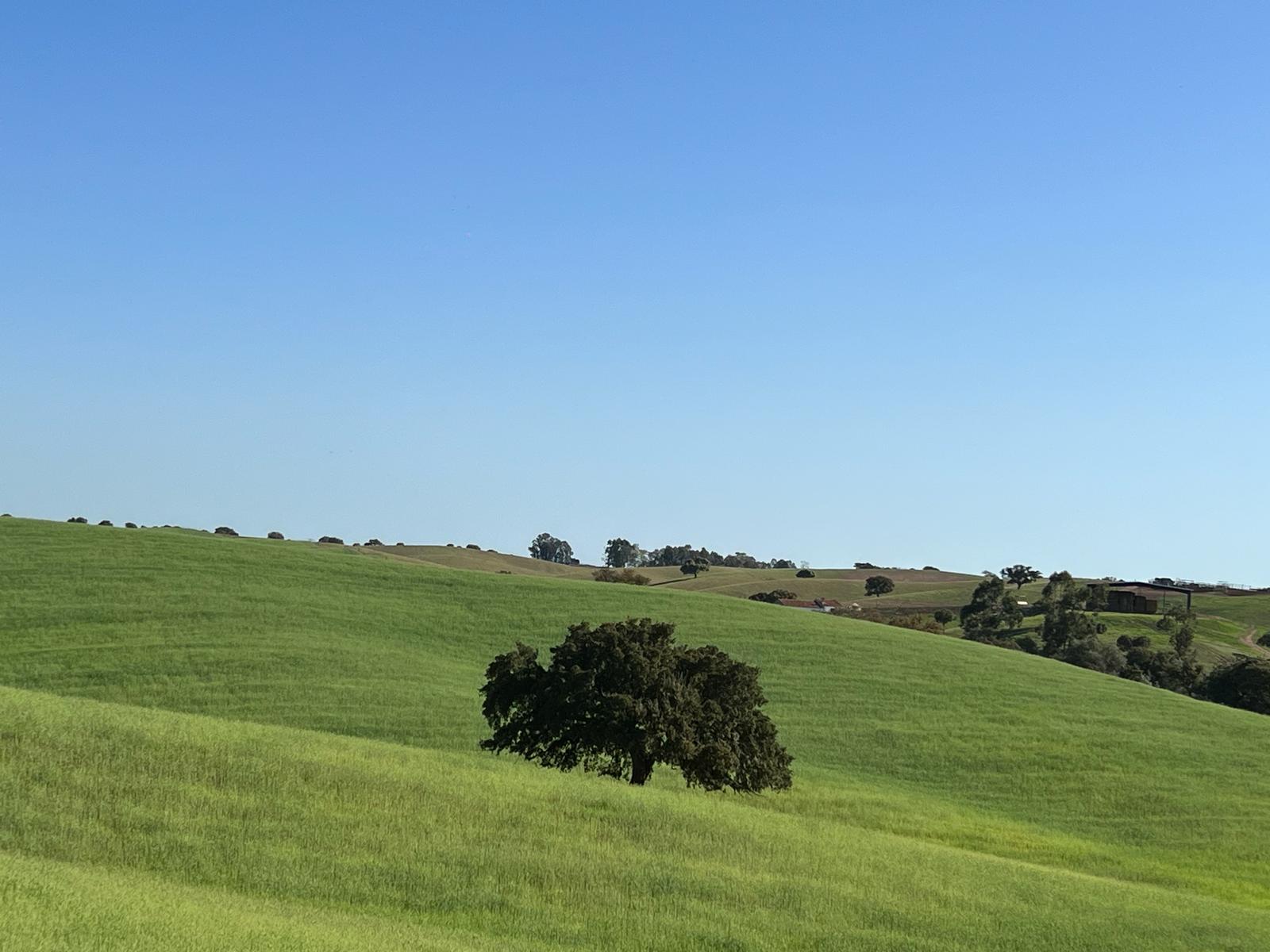

1 – Design, modeling and development
After the briefing with the client, the models are developed internally in the technical office, where the design and rigorous monitoring of the prototype is carried out throughout the various phases of the manufacturing process. After approval, the order will be produced.
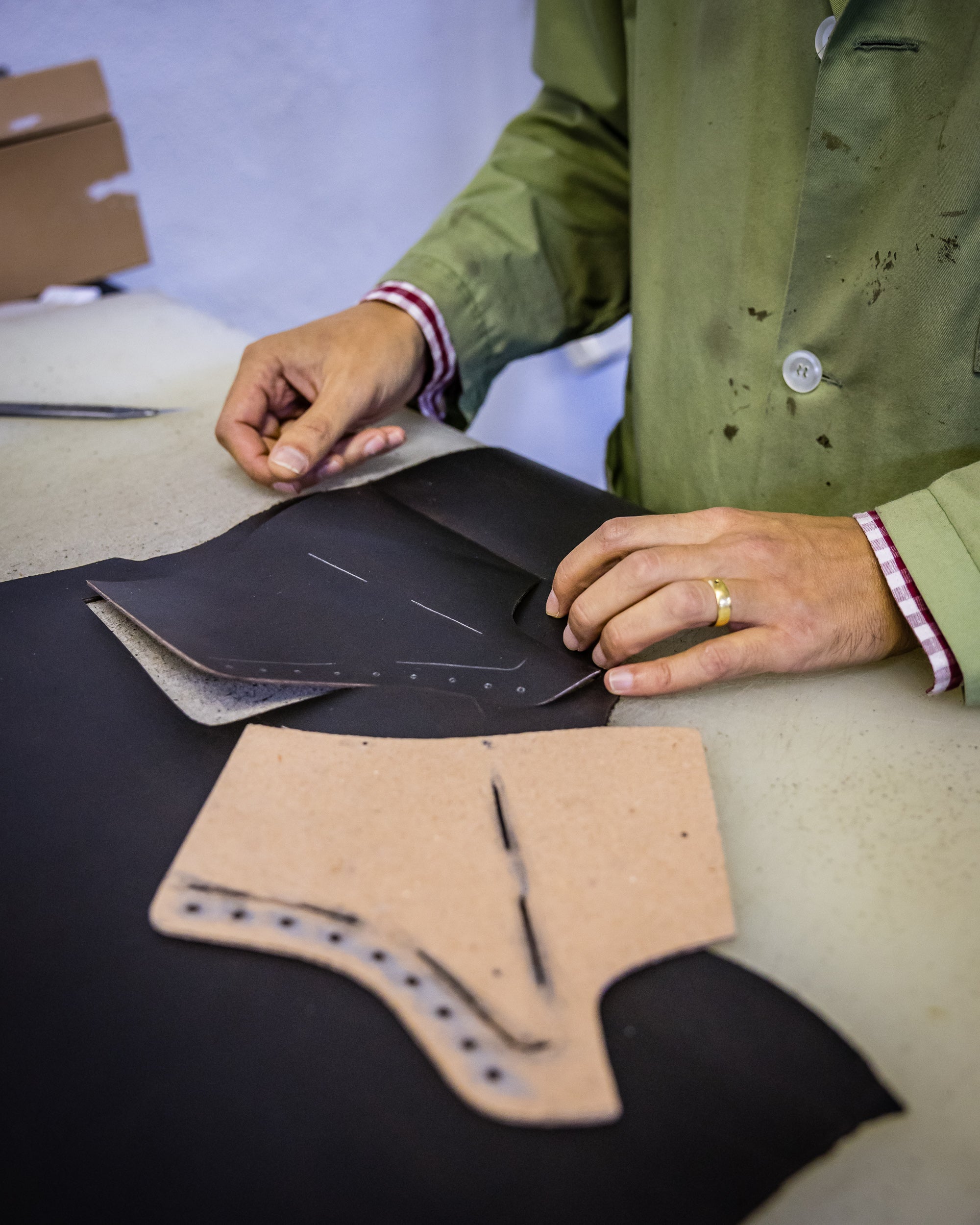
2 – Selection of raw material
Strict control is carried out on all leathers and other components to ensure that they are the most suitable for the type of footwear to be manufactured.
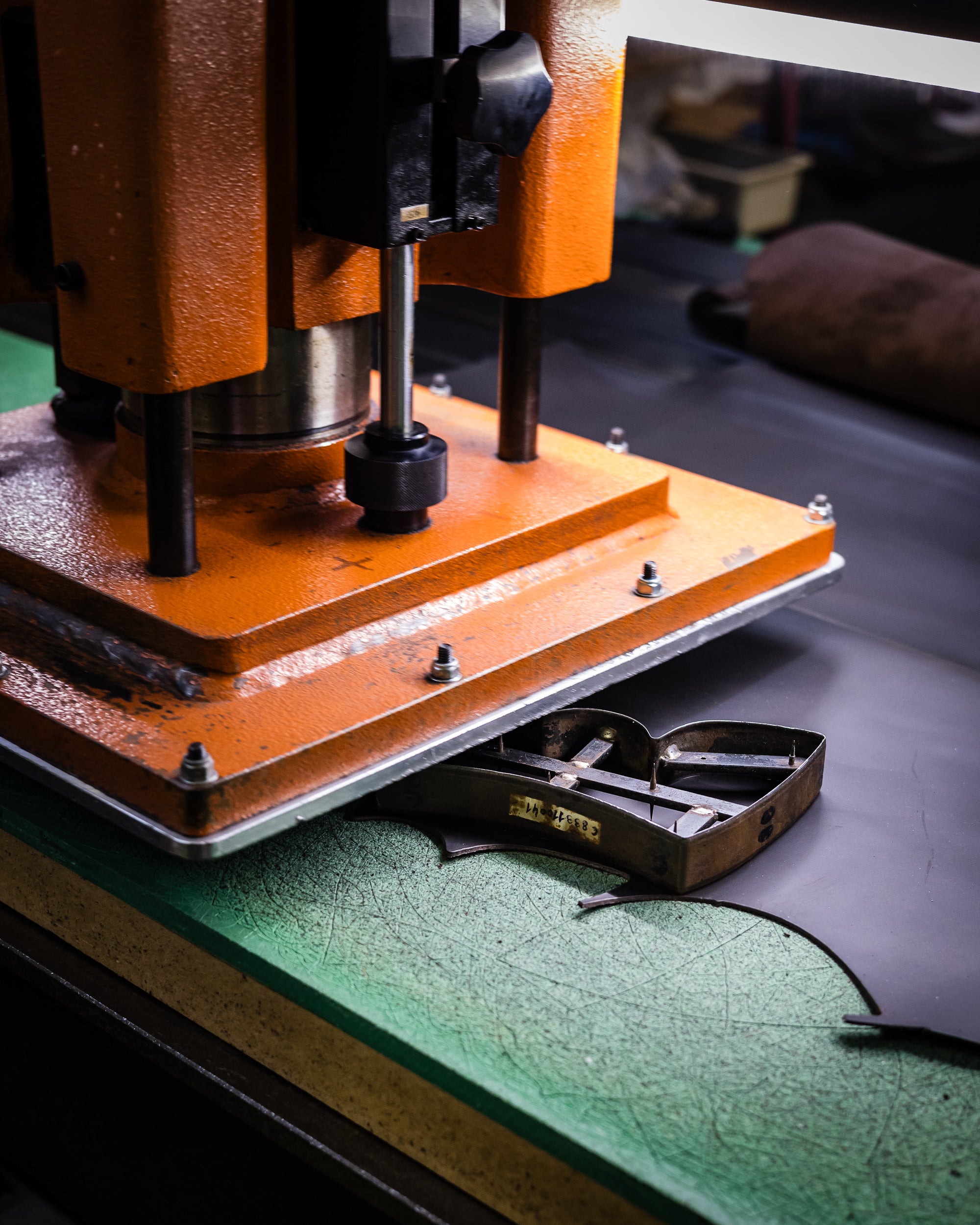
3 – Cut
The skins must be cut by a specialist so that each piece is cut from the appropriate area of skin so that it can then be molded correctly to the shape of the foot.
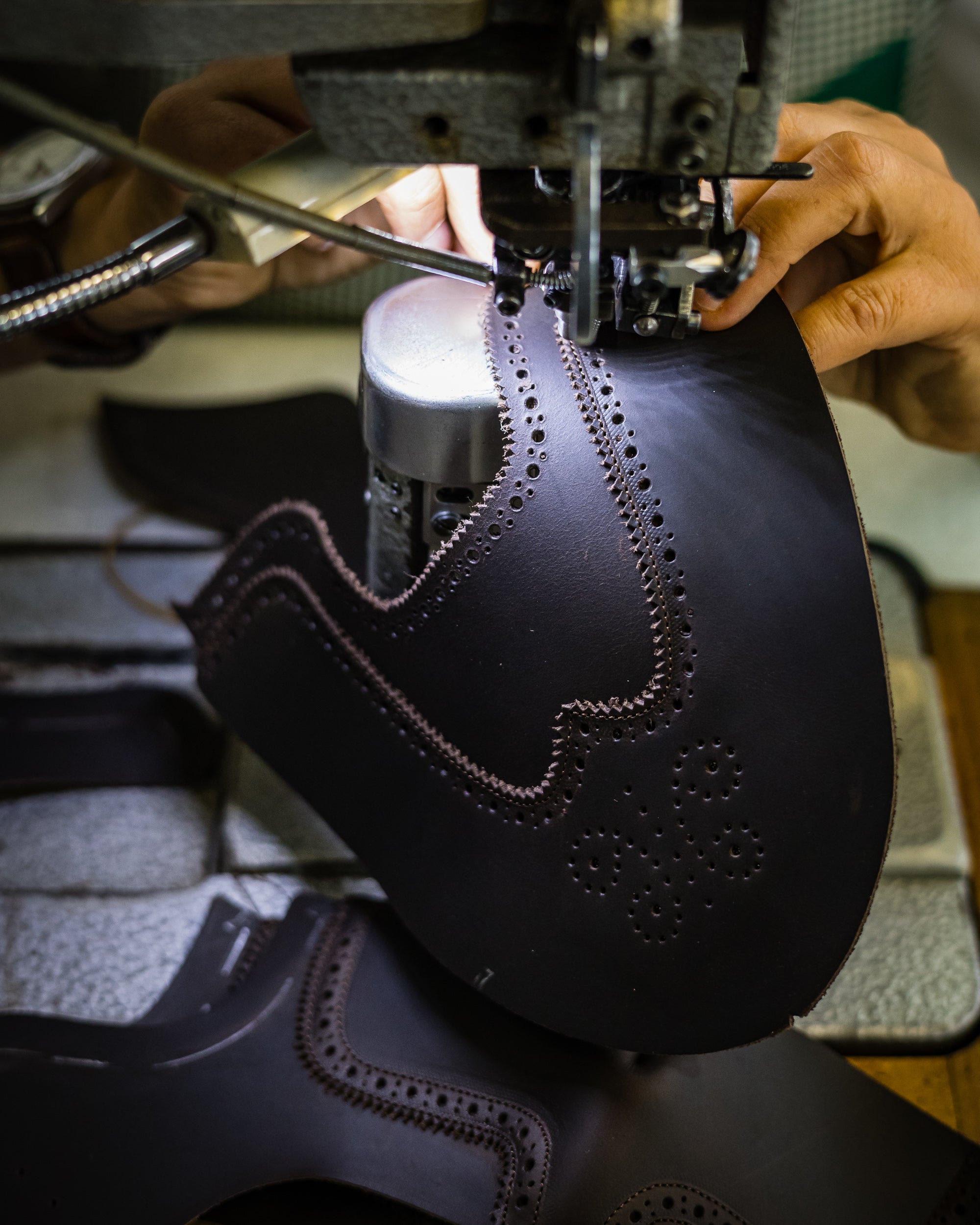
4 – Sewing
The joints of all the cut leather pieces are sewn together to form, as a whole, the upper part of the shoe.

5 – Assembly
The upper part of the shoe, already sewn, is assembled into the shape of the foot where it is joined to the vegetable leather insole, already deflowered and previously prepared for sewing. This is followed by the “Insoled Seam” in which the insole is joined to the upper part of the shoe with a leather strip called a vira.
The “box” under the insole, approximately 4mm high, is filled with flexible cork that allows the foot to adapt correctly to the shoe, whilst absorbing the sweat released.
A sole is then placed and sewn on the turn with natural threads, followed by the thinning and preparation of the sole and heel as well as removing the shoe from its shape.
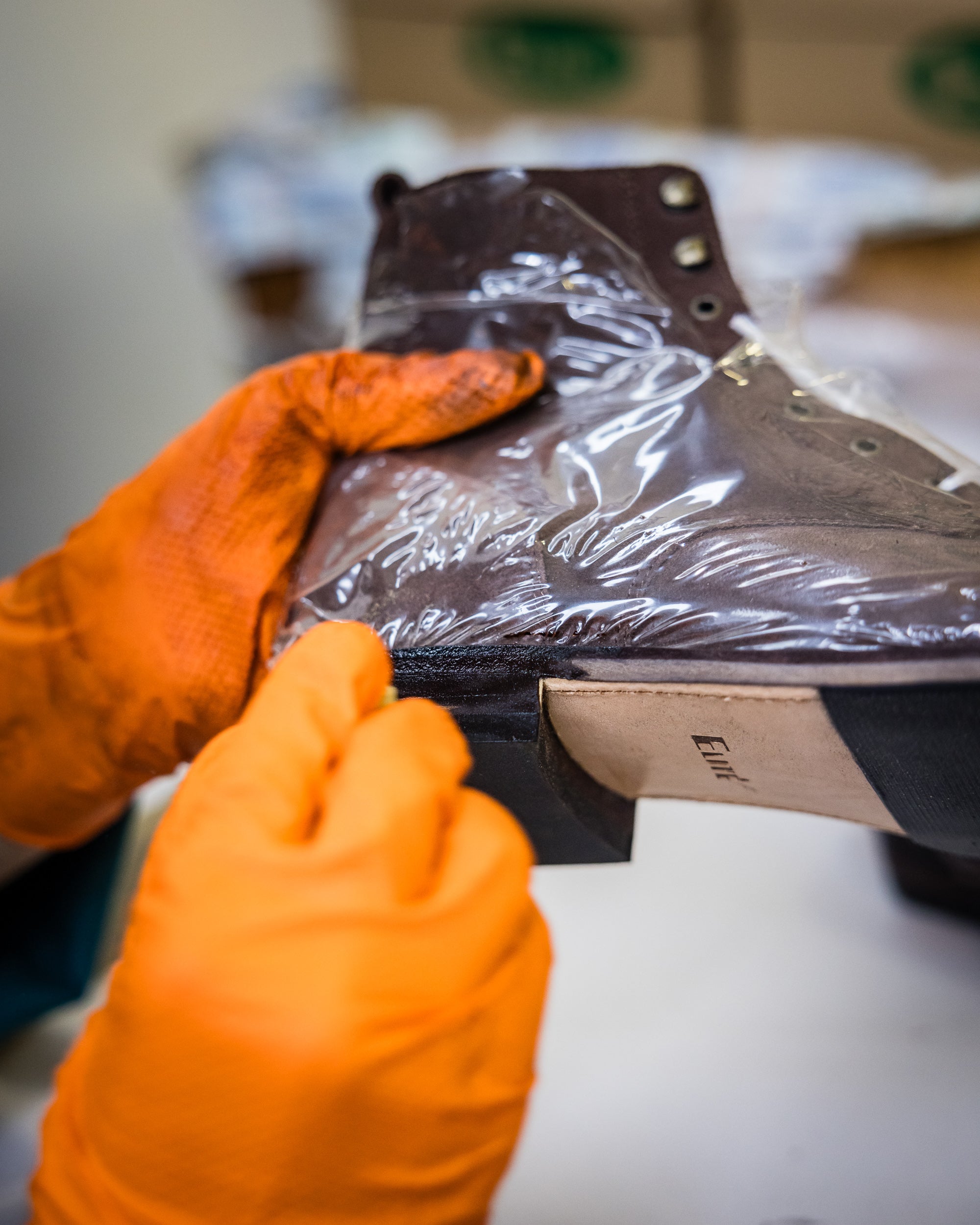
6 – Finishing
The edge of the shoe is painted with ecological paints and natural waxes are used to finish the treads, while the upper part is finished with putties and polished with wool brushes to give the shoe a uniform and smooth touch.
After a rigorous final inspection, the footwear is packed in the appropriate box and accessories can be incorporated for better maintenance.
GOODYEAR WELTED FOLK
The “Goodyear Welted” construction is an ancestral art passed down from generation to generation and stands out as being the most complex and highest quality method.
At the end of the 19th century, in order to industrialize this footwear, Mr. Charles Goodyear Jr. would invent the first machine that would excellently combine manual and industrial work to carry out such a distinct method.
and excellence.
Portugal is one of the few countries that has mastered the art of Goodyear insoles and that relies on the hands and unique mastery of our artisans, this being a process chosen par excellence by us.
The word Goodyear comes from the name of the inventor, while “Welt” is the English word for “turn” , that is, piece of strip
in leather .
The machine developed by Mr. Chalres Goodyear Jr. was able to sew the binding to the upper part of the sole and the mounting insole, creating an attachment point.
Once the sole and midsole are joined to the leather, a second machine will sew them back together.
This is a revolutionary process that until then had been carried out manually by artisans in a slow and arduous way.
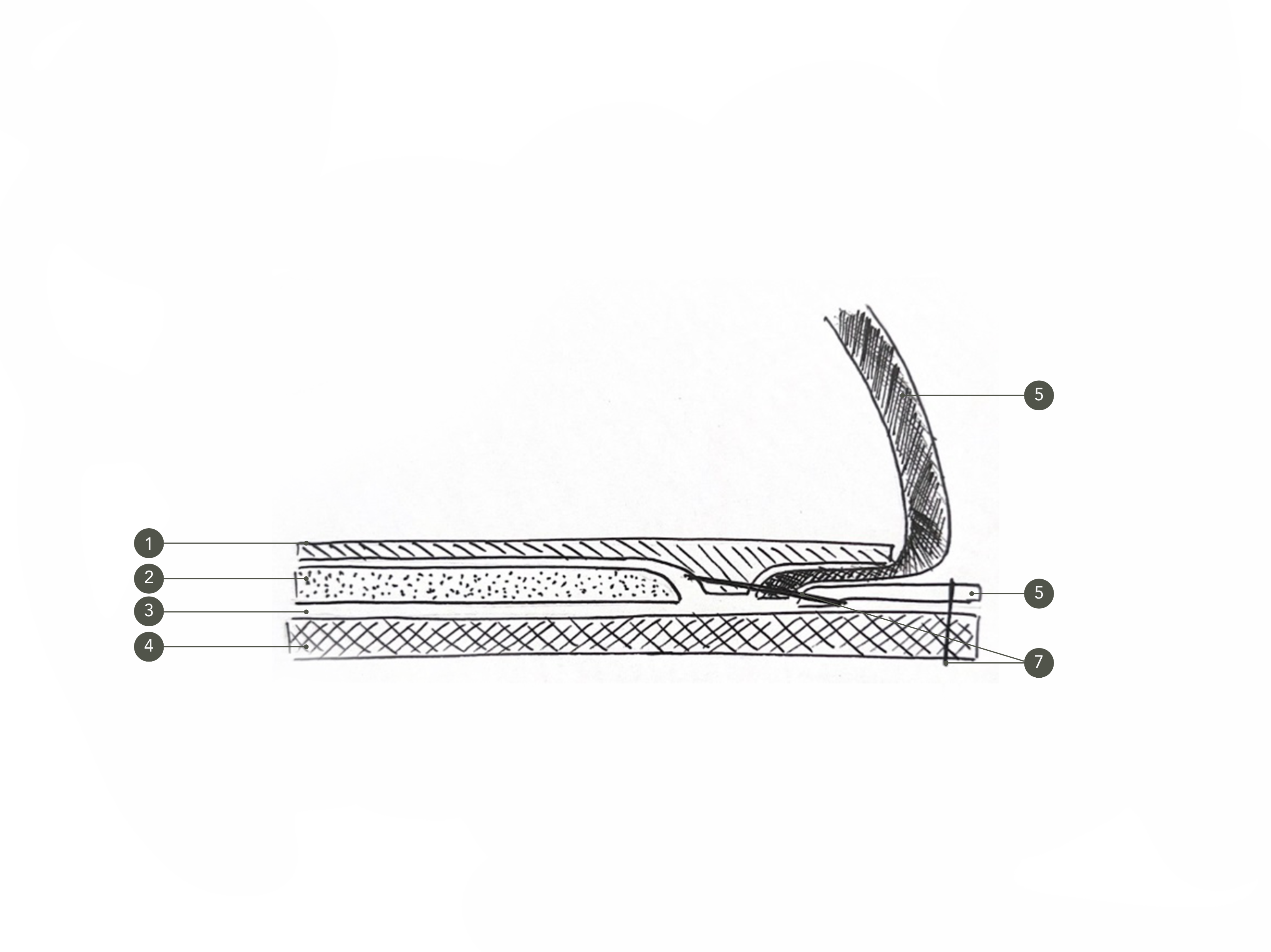
1. Insole
2. Cork
3. Midsole
4. Sole
5. Upper Skin
6. Flip
7. Sewn
Shoe Fitting Systems
In 1856, a sewing machine was invented by Lyman Blake and perfected in 1864, giving rise to the designation of the type of construction.
The equipment most used to carry out this operation is from the Blake brand.
In this construction system there is a direct fixation of the cut to the sole through a sewing process, in the toecap and flank areas, using this specific equipment.
The quality and flexibility of this type of construction process are points in favor of a lighter and lighter type of footwear, offering a feeling of comfort and freshness in warmer climates, whilst maintaining the demanding quality standards.
Process similar to Goodyear Welted in the initial phase, with significant changes during the assembly process.
In this construction system, the cut is directly attached to the sole through a sewing process using specific equipment and then the complete midsole is sewn and then turned to sew to the sole.
This method is most similar to Goodyear and is used in our Tubular Loafers .
This process is identical to the traditional “Goodyear” , but with the seam sewn to the skin
“L” shaped.
It is used for high-resistance mountain, riding and casual footwear .
System technically developed for “Goodyear Welted” summer footwear, as it makes the footwear very light and comfortable.
It uses the same manufacturing system as Goodyear Welted, with the replacement of some components:
1. The leather insole is very flexible
2. The insulation of the lower part is made on the back with flexible cork and on the front with special absorbent foam
3. The leather sole is tanned with special vegetable compounds to make it very flexible and durable
This process undergoes changes during the assembly process.
Using the same raw material, the same cutting and sewing , the upper part of the shoe is assembled directly onto the insole, which is also sewn directly to the midsole, thus obtaining a more economical alternative to Goodyear Welted .
This process, like the previous ones, also undergoes changes during the assembly process.
Also using the same raw material, the same cutting and sewing, the upper part of the shoe is assembled directly onto the insole, which is also sewn directly to the midsole, a turn is placed and sewn, thus obtaining an alternative to imitate. the Goodyear Welted, but more economical.